Magnesium alloy is an alloy based on magnesium with other elements added. Its characteristics are: small density (about 1.8g/cm3), high strength, large elastic modulus, good heat dissipation, good shock absorption, impact load capacity than aluminum alloy, good corrosion resistance of organic matter and alkali. The main alloying elements are aluminum, zinc, manganese, cerium, thorium and a small amount of zirconium or cadmium. The most widely used alloys are magnesium and aluminum, followed by magnesium and manganese and magnesium, zinc and zirconium. Mainly used in aviation, aerospace, transportation, chemical, rocket and other industrial sectors.
features
Low density, good specific performance, good shock absorption performance, good electrical and thermal conductivity, good process performance, poor corrosion resistance, easy oxidation and combustion, poor heat resistance.
Its processing process and corrosion and mechanical properties have many characteristics: fast heat dissipation, light weight, good rigidity, with a certain corrosion resistance and dimensional stability, impact resistance, wear resistance, good attenuation performance and easy recovery; In addition, there are high thermal and electrical conductivity, non-magnetic, good shielding and non-toxic characteristics.
Application: Magnesium alloy is widely used in portable equipment and automotive industry to achieve the purpose of lightweight.
Product features
The processing process and corrosion and mechanical properties have many characteristics: fast heat dissipation, light weight, good rigidity, corrosion resistance and dimensional stability, impact resistance, wear resistance, good attenuation performance and easy to recover; In addition, there are high thermal and electrical conductivity, non-magnetic, good shielding and non-toxic characteristics.
Application: Magnesium alloy is widely used in portable equipment and automotive industry to achieve the purpose of lightweight.
Although the specific gravity of magnesium alloy is heavier than that of plastic, its strength and elasticity per unit weight are higher than that of plastic. Therefore, under the condition of parts with the same strength, magnesium alloy parts can be thinner and lighter than plastic parts. In addition, because the specific strength of magnesium alloy is also higher than that of aluminum alloy and iron, the weight of aluminum or iron parts can be reduced without reducing the strength of the parts.
The magnesium alloy has the highest relative strength (ratio of strength to mass). Specific stiffness (stiffness to mass ratio) is close to aluminum alloy and steel, much higher than engineering plastics.
In the elastic range, the energy absorbed by the magnesium alloy under the impact load is half as large as that of the aluminum alloy, so the magnesium alloy has good seismic and noise reduction performance.
The melting point of magnesium alloy is lower than that of aluminum alloy. The tensile strength of magnesium alloy castings is similar to that of aluminum alloy castings, generally up to 250 MPa, and the highest up to more than 600 MPa. The yield strength and elongation are not much different from those of aluminum alloy.
Magnesium alloy also has good corrosion resistance, electromagnetic shielding performance, radiation resistance performance, can be 100% recycling.
The stability of magnesium alloy parts is higher than that of high pressure castings, so it can be machined with high precision.
Magnesium alloy has good die casting performance, and the minimum wall thickness of die casting can reach 0.5mm. It is suitable for manufacturing all kinds of die casting parts for automobiles.
However, the linear expansion coefficient of magnesium alloy is very large, reaching 25 ~ 26 μm/m℃, while that of aluminum alloy is 23 μm/m℃, brass is about 20 μm/m℃, structural steel is about 12 μm/m℃, cast iron is about 10μm/m℃, rock (granite, marble, etc.) is only 5 ~ 9 μm/m℃, glass is 5 ~ 11 μm/m℃.
Magnesium alloy is an alloy based on magnesium with other elements added. Its characteristics are: small density, high specific strength, large elastic modulus, good shock absorption, impact load capacity than aluminum alloy, good corrosion resistance. The main alloying elements are aluminum, zinc, manganese, cerium, thorium and a small amount of zirconium or cadmium. The most widely used alloys are magnesium and aluminum, followed by magnesium and manganese and magnesium, zinc and zirconium.
Magnesium alloys have the lightest specific gravity of all structural alloys, so the weight of aluminum or iron components can be reduced without reducing the strength of the components. The specific strength of magnesium alloy is obviously higher than that of aluminum alloy and steel, and the specific stiffness is similar to that of aluminum alloy and steel. In the elastic range, the energy absorbed by the magnesium alloy under the impact load is larger than that of the aluminum alloy, so the magnesium alloy has good seismic and noise reduction performance. Under the same load, the damping property is 100 times that of aluminum and 300 ~ 500 times that of titanium alloy. The enclosure of 3C products (mobile phones and computers) should be able to provide superior anti-electromagnetic protection, while the enclosure of magnesium alloy can fully absorb electromagnetic interference with frequencies over 100dB. Excellent texture. Magnesium alloy has excellent appearance and touch texture, which makes the product more luxurious and less susceptible to corrosion in the air.
Compared with alloy, magnesium alloy has an absolute advantage in heat dissipation. For radiators made of magnesium alloy and aluminum alloy with the same volume and shape, the heat (temperature) produced by a heat source is more easily transferred from the root of the heat sink to the top speed than aluminum alloy, and the top is more easily reached to high temperature. That is, the temperature difference between the root and top of the radiator of aluminum alloy material is smaller than that of the radiator of magnesium alloy material. This means that the temperature difference between the air temperature at the root and the air temperature at the top of the radiator made of magnesium alloy material is larger than that of the radiator made of aluminum alloy material, so the diffusion and convection of the air inside the radiator is accelerated, and the cooling efficiency is improved. Therefore, the heat dissipation time of magnesium alloy is less than half of that of aluminum alloy at the same temperature.
Therefore, magnesium alloys are ideal materials for LED and other lighting applications, automotive application parts, and other parts that require high quality, high strength, and high toughness.
Designation |
1 Al |
8 Be |
7 Cu |
5 Fe |
3 Mn |
6 Ni |
Rare Earth |
4 Si |
Stontrum |
2 Zn |
Other Metallic impurities,max |
Other Impurities,max |
AZ91D |
8.5~9.5 |
0.0005-0.0015 |
0.025 |
0.04 |
0.17-0.050 |
0.001 |
|
0.08max |
|
0.45-0.9 |
0.01 |
|
AM60B |
5.6~6.4 |
0.0005-0.0015 |
0.008 |
0.04 |
0.26-0.50 |
0.001 |
|
0.08max |
|
0.20max |
0.01 |
|
AM50A |
4.5~5.3 |
0.0005-0.0015 |
0.008 |
0.04 |
0.28-0.50 |
0.001 |
|
0.08max |
|
0.20max |
0.01 |
|
AZ63A |
5.5~6.5 |
... |
0.20 |
-0.00035 |
0.15-0.35 |
0.010 |
|
0.20 |
|
0.27-3.3 |
|
0.30 |
AS41B |
3.7~4.8 |
0.0005-0.0015 |
0.015 |
0.0035 |
0.35-0.6 |
0.001 |
|
0.60-1.4 |
|
0.10max |
0.01 |
|
AZ91A |
8.5~9.5 |
... |
0.08 |
... |
0.15-0.40 |
0.01 |
|
0.20max |
|
0.45-0.9 |
|
0.30 |
AZ91B |
8.5~9.5 |
... |
0.25 |
... |
0.15-0.40 |
0.01 |
|
0.20max |
|
0.45-0.9 |
|
0.30 |
AJ62A |
5.6~6.6 |
0.0005-0.0015 |
0.008 |
0.004 |
0.26-0.50 |
0.001 |
|
0.08 |
2.1-2.8 |
0.20max |
0.01 |
|
AS21A |
1.9`2.5 |
0.0005-0.0015 |
0.008 |
0.004 |
0.2-0.5 |
0.001 |
|
0.7-1.2 |
|
0.20max |
0.01 |
|
AS21B |
1.9`2.5 |
0.0005-0.0015 |
0.008 |
0.0035 |
0.05-0.15 |
0.001 |
0.06-0.25 |
0.7-1.2 |
|
0.25max |
|
|
AS41A |
3.7~4.8 |
|
0.004 |
|
0.22-0.48 |
0.01 |
|
0.60-1.4 |
|
0.10max |
|
0.30 |
AS91C |
8.3~9.2 |
|
0.008 |
|
0.15-0.35 |
0.010 |
|
0.20 |
|
0.45-0.9 |
|
0.30 |
AZ91E |
8.3~9.2 |
|
0.015 |
0.005 |
0.17-0.50 |
0.0010 |
|
0.20 |
|
0.45-0.9 |
0.01 |
0.30 |
镁合金非国标89.109% |
9.5922 |
<0.0000 |
0.0637 |
<0.0044 |
0.0885 |
0.0075 |
|
0.3447 |
|
0.7900 |
|
|
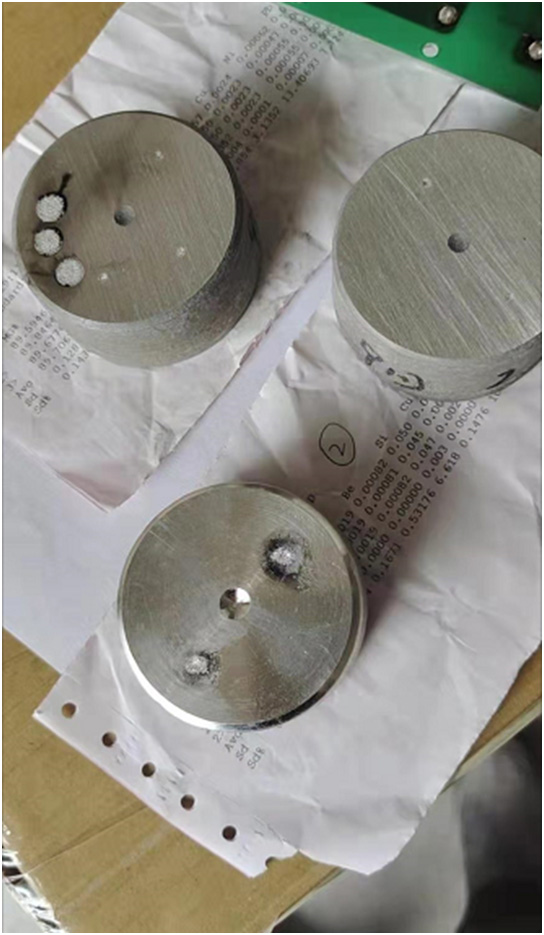
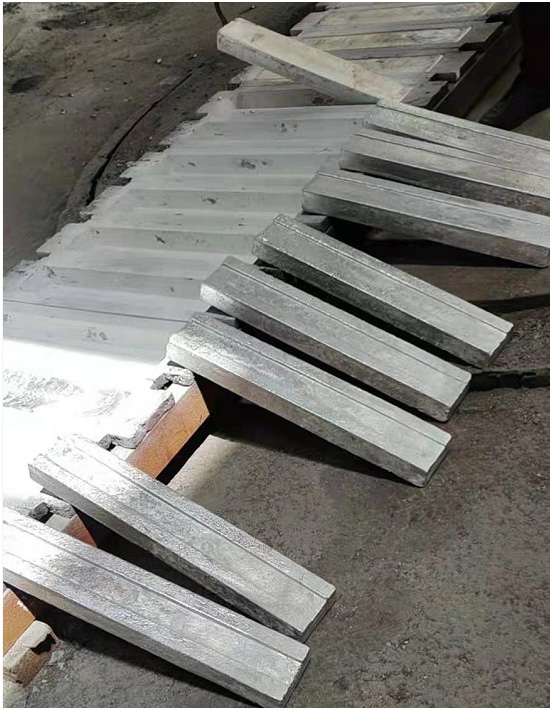
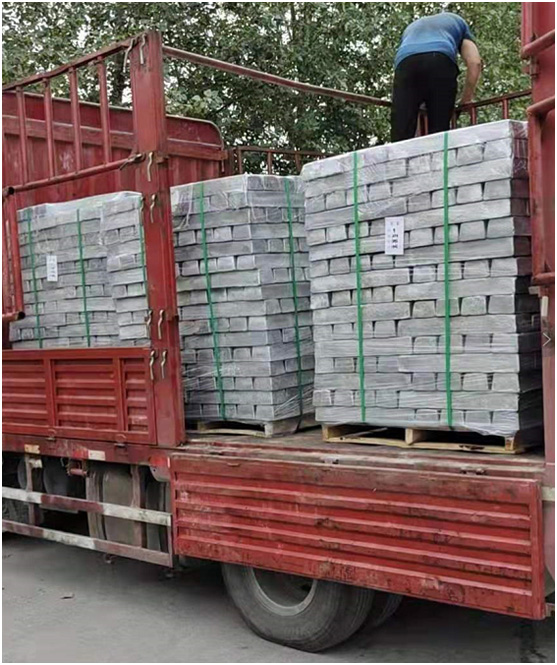